Backward Integration Explained – with Real Industry Examples
Definition of Backward Integration
Backward integration is a business strategy where a company expands its operations to control or acquire its suppliers. This means that instead of relying on external suppliers for raw materials or components, the company produces these inputs itself. This also means that the company gains control of the business activities that were behind in its value chain. By doing so, the company can reduce costs, ensure a more reliable supply chain, improve quality control, and gain more control over the production process.
For example, a watch manufacturer might acquire a company that produces watch movements or components, ensuring a steady supply of essential parts and potentially lowering production costs.
How does Backward Integration Work?
Backward integration is where the company acquires or starts another new company that supplies the products or services required to fulfill its manufacturing process. The company gains control over the raw materials using the backward integration method.
Backward integration is also known as when a company expands across multiple supply chain segments, which are behind its value chain, to control a part or entire production process. This is a form of vertical integration, where the company performs tasks that were formerly performed by its suppliers.
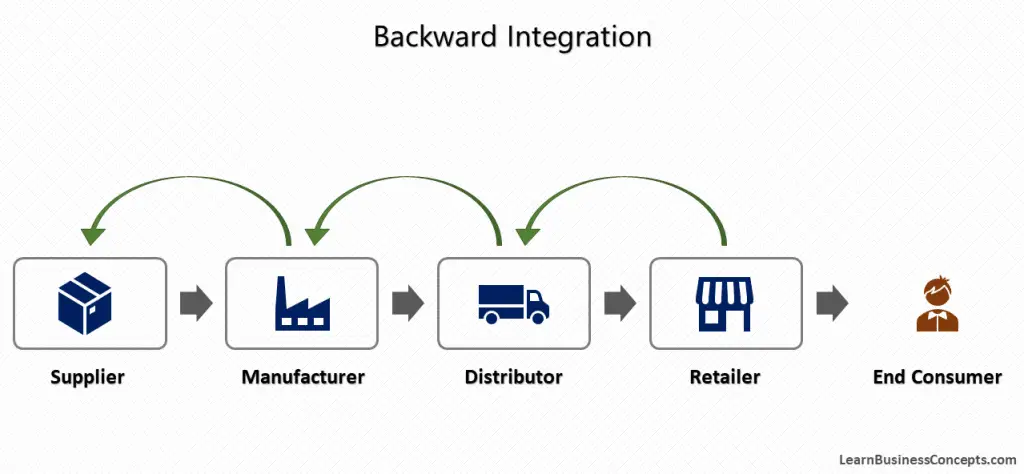
Why do Companies Follow Backward Integration?
1. Cost Reduction
Backward integration allows companies to reduce costs by eliminating supplier markups and gaining control over the production of raw materials or components. By producing essential inputs internally, companies can achieve significant savings and enhance their profit margins. For example, a car manufacturer that produces its own steel can avoid the costs associated with purchasing it from external suppliers.
2. Supply Chain Stability
Ensuring a steady and reliable supply of critical inputs is a major reason for backward integration. By owning or controlling suppliers, companies can mitigate risks related to supply chain disruptions, such as delays, shortages, or quality issues. This stability is crucial for maintaining consistent production schedules and meeting customer demand.
3. Quality Control
Backward integration provides greater control over the quality of raw materials and components used in production. Companies can implement stringent quality assurance processes to ensure that inputs meet their standards, resulting in higher-quality end products. This control can enhance the company’s reputation and customer satisfaction.
4. Competitive Advantage
Companies can differentiate themselves from competitors who rely on third-party suppliers by integrating backward. This integration can lead to proprietary processes or materials that provide a competitive edge. For instance, a tech company developing its own microchips may create unique features that set its products apart in the market.
5. Increased Bargaining Power
Controlling key aspects of the supply chain can enhance a company’s bargaining power with external suppliers. Even if a company does not produce all its own inputs, having the capability to do so can serve as leverage in negotiations, leading to better terms and prices from remaining suppliers.
6. Innovation and Customization
Backward integration can foster innovation by providing more control over the entire production process. Companies can experiment with new materials, technologies, and processes, leading to unique product offerings. Additionally, this control allows for greater customization to meet specific customer needs or market demands.
7. Market Expansion
Integrating backward can support market expansion by ensuring that key inputs are available to meet increased production needs. As companies grow and enter new markets, having control over the supply chain helps maintain the scalability of operations without being constrained by supplier limitations.
8. Better Coordination
Owning multiple stages of the supply chain can improve coordination and communication across different parts of the business. This integration can lead to more efficient operations, reduced lead times, and better alignment of production schedules with market demands.
9. Reduced Dependence on External Suppliers
Backward integration reduces a company’s dependence on external suppliers, which can be particularly advantageous in volatile markets or regions with unstable political or economic conditions. This autonomy helps safeguard the company against external risks that could impact the availability or cost of key inputs.
10. Long-term Strategic Investment
Backward integration can be a strategic investment for long-term growth and sustainability. By investing in upstream capabilities, companies can build a robust and self-sufficient supply chain that supports their future expansion and adaptability to market changes.
Real Industry Examples of Backward Integration
1. Netflix Started their Own Production and Shows
Netflix originally started with renting DVDs through mail service. It was originally a content distributor, has integrated backward by producing its own content through Netflix Originals. By creating its own movies and series, Netflix reduces reliance on third-party studios, ensures a steady stream of unique content, and retains full control over the production process and intellectual property.
Netflix then started to develop their own production and shows which is a real-world industry example for backward integration.
More information and reference: History of Netflix- Founding, Model, Timeline, Milestones – vdocipher.com
2. Continental acquired Veyance Technologies in 2015
Continental is an international automotive supplier and tyre manufacturer. Veyance Technologies was a manufacturer of rubber products for industrial companies. Continental expects to expand its global position in rubber and plastics technologies and further increase the proportion of industrial and end-customer sales.
More information on this acquisition: News Published in continental.com, Article Published in im-mining.com, Paper of Backward and Forward Integration.
3. Amazon started “Amazon Publishing”
In 1995 Amazon started as an online book retailer (internet bookstore) procuring books from publishers. In 2009 Amazon started “Amazon Publishing” which allows them to publish books. After the above, Amazon may receive a cut on both as publisher and as bookseller if a reader buys one of its titles.
More information on this acquisition:” The Amazon Publishing Juggernaut” – Article Published in The Atlantic, “How To Self-Publish Your Book Through Amazon” – Article Published in Forbes
4. Acer acquires stake in a venture of Texas Instruments
Acer’s product range includes laptop and desktop PCs, tablets, smartphones, monitors, projectors, etc. The synergies of this business activity were to produce semiconductors and additional electronic components.
More information on this acquisition: News Published in EE Times, News Published in the Wall Street Journal, Paper of Backward and Forward Integration.
5. Carnegie Steel Company constructed its Own Blast Furnaces
Carnegie Steel Company is a steel-producing company. The company needs ‘coke’ to produce steel. Several nearby suppliers own ‘blast furnaces’ to produce coke. However, these suppliers were unable to consistently meet the demand for Carnegie’s mills. Then the company moved to construct its own ‘blast furnaces’ for coke production, cutting out the dependency on their suppliers and ensuring reliable and cheap supply.
More information: Article Published about “Carnegie Steel” in Harvard Business School Digital Initiative
6. Ford Motor Company
Ford is a classic example of backward integration. In the early 20th century, Ford owned rubber plantations in Brazil, iron mines, and glassworks to supply its car manufacturing operations. This strategy ensured a steady supply of key materials and allowed Ford to control costs and quality more effectively.
7. Starbucks
Starbucks has pursued backward integration by buying coffee farms. This strategy helps Starbucks ensure the quality and sustainability of its coffee supply, reduce costs, and gain greater control over the entire supply chain, from bean to cup.
8. Apple Inc.
Apple integrates backward by designing its own microchips and other components for its devices. By developing the A-series chips used in iPhones and iPads, Apple enhances performance, differentiates its products, and reduces dependence on external suppliers like Intel or Qualcomm.
9. Toyota
Toyota has implemented backward integration by producing its own steel through subsidiaries like Toyota Tsusho. This strategy ensures a reliable supply of high-quality steel for its automotive manufacturing, reduces costs, and enhances control over the production process.
10. Samsung
Samsung integrates backward by manufacturing many of the components used in its electronic products, such as semiconductors, displays, and batteries. This vertical integration allows Samsung to innovate rapidly, ensure component quality, and maintain competitive pricing.
How Company Grows with Backward Integration
Backward integration can be a strategic pathway for a company to foster growth and enhance its competitive position through several key steps as described following,
- Strategic Planning and Assessment
The journey begins with strategic planning and assessment of the company’s supply chain needs and capabilities. This involves identifying critical components or raw materials that are currently sourced externally and evaluating the potential benefits of producing them in-house. For example, a watch manufacturer might assess the feasibility of producing its own watch movements to reduce dependency on external suppliers and improve production efficiency. - Acquisition or Development of Production Facilities
Once the decision is made to pursue backward integration, the company may choose to acquire existing suppliers or develop its own production facilities. Acquisitions can provide immediate access to expertise, technology, and established market presence, while internal development allows for tailored solutions aligned with the company’s specific requirements. For instance, acquiring a company specializing in watch movement production or building a dedicated facility can enable the watch manufacturer to control quality and streamline production processes. - Implementation of Quality Control Measures
Implementing stringent quality control measures becomes crucial with production capabilities in place. The company establishes standards and protocols to ensure that the manufactured components meet high-quality standards consistent with its brand reputation. This step not only enhances product quality but also boosts customer confidence and satisfaction. - Cost Efficiency and Supply Chain Optimization
Backward integration typically results in cost savings by eliminating supplier markups and reducing logistics costs associated with external procurement. By optimizing the supply chain, the company improves operational efficiency and financial performance. For example, producing components internally can lead to lower production costs and improved profit margins, contributing to overall growth and sustainability. - Enhanced Innovation and Flexibility
Controlling production processes empowers the company to innovate more freely. With in-house capabilities, the company can experiment with new materials, technologies, and production methods. This fosters continuous improvement and innovation, allowing the company to stay ahead in a competitive market landscape. Moreover, the flexibility gained from internal production enables quicker response to market demands and changes in consumer preferences. - Strategic Differentiation and Competitive Advantage
Over time, backward integration can position the company uniquely in the market. By offering products with superior quality, reliability, and innovation, the company strengthens its competitive advantage. Customers recognize the value of vertically integrated products, which may command premium pricing and increase market share. This strategic differentiation not only drives growth but also solidifies the company’s market position against competitors.
In summary, backward integration supports company growth by strategically aligning production capabilities with business objectives, enhancing operational efficiency, fostering innovation, and establishing a competitive edge in the marketplace. Each step in the process contributes to building a robust, sustainable business model that can adapt and thrive in dynamic market conditions.
Key Benefits / Advantages of Backward Integration
The backward integration method will result in many benefits to the company such as cost savings, increased revenues, and improved efficiency in the production process. Following are some key benefits of backward integration,
1. Cost Reduction
Backward integration can lead to significant cost savings for a company. The company can reduce the costs associated with purchasing from suppliers by producing its own raw materials or components. This also eliminates the middleman, which can further reduce expenses. For example, if a watch manufacturer integrates backward by acquiring a supplier of watch movements, it can save on the costs of purchasing these components from third-party suppliers.
2. Improved Supply Chain Control
When a company controls its supply chain, it can ensure a more reliable and consistent supply of essential materials. This reduces the risk of disruptions caused by supplier issues, such as delays or shortages. For instance, a watchmaker that produces its own components can avoid production halts due to supplier problems, ensuring that its production process runs smoothly.
3. Enhanced Quality Control
By integrating backward, a company can maintain higher standards of quality control over the materials and components it uses. This is because the company can directly oversee the production processes and implement its quality standards. For a watch manufacturer, this means it can ensure that every part of its watches meets its precise specifications, resulting in a higher-quality final product.
4. Increased Profit Margins
Owning the supply chain allows a company to capture more profit by eliminating the markups that suppliers typically add to their prices. This can lead to higher profit margins on the company’s products. For example, a watchmaker that produces its own components can sell its watches at the same price as before but with lower production costs, resulting in higher profits.
5. Competitive Advantage
Backward integration can give a company a competitive edge in its industry. The company can differentiate itself from competitors, offer unique products, and respond more quickly to market changes by controlling more aspects of the production process. A watch manufacturer that controls its own component production can innovate more rapidly and introduce new designs faster than competitors who rely on external suppliers.
Key Drawbacks / Disadvantages of Backward Integration
1. High Initial Costs
Implementing backward integration often requires substantial investment. Acquiring or setting up production facilities, purchasing equipment, and training employees can be expensive. This high initial cost can strain a company’s finances, especially if the expected benefits do not materialize quickly.
2. Reduced Flexibility
Backward integration can reduce a company’s flexibility to adapt to market changes. A company may find it harder to switch suppliers or change production methods in response to new technologies or shifts in consumer preferences by committing to producing its own materials or components.
3. Complexity in Management
Managing a larger, more integrated supply chain can be complex and challenging. The company needs to oversee additional stages of production, which can require different expertise and management skills. This increased complexity can lead to inefficiencies and higher administrative costs.
4. Risk of Overcapacity
If a company integrates backward and its production facilities produce more than needed, it might face overcapacity issues. This can result in higher operational costs and wasted resources if the excess production cannot be sold or efficiently utilized.
5. Focus Diversion
Backward integration can divert a company’s focus from its core competencies. The company might spread its resources too thin, potentially compromising its ability to innovate and excel in its primary business areas by taking on additional production processes.
6. Supplier Relationships
Existing supplier relationships can be adversely affected by backward integration. Suppliers who are no longer needed might become competitors or refuse to cooperate in other areas. Additionally, the company loses the benefits of supplier specialization and expertise, which can sometimes lead to better quality or more cost-effective solutions than in-house production.
Effects of Backward Integration
Backward integration can significantly enhance a company’s cost efficiency, supply chain reliability, and quality assurance. By producing its own raw materials or components, a company can reduce production costs and ensure a consistent supply of inputs, mitigating the risks of supply chain disruptions. This control over the supply chain also allows for stringent quality control measures, leading to higher-quality products. Additionally, backward integration can increase a company’s bargaining power with suppliers and foster innovation, as the company can experiment with new processes and technologies more easily.
However, backward integration also introduces substantial financial and operational risks. The initial capital investment required for acquiring or setting up production facilities can be significant, potentially straining the company’s finances. Furthermore, managing an expanded supply chain increases operational complexity and can lead to inefficiencies if not handled properly. Companies must carefully weigh these risks against the potential benefits to determine if backward integration is a strategic fit for their business objectives.
Difference between Acquisition Strategy and In-House Build
An acquisition strategy involves a company purchasing another company or its assets to quickly gain new capabilities, access to markets, or resources. This approach is often used to achieve backward integration by acquiring suppliers or manufacturers of essential components. For example, a watch manufacturer might acquire a company that specializes in producing high-quality watch movements, thus securing a reliable source of these components and integrating the production process. The primary advantages of an acquisition strategy include speed and the immediate availability of proven processes and technologies. It allows the acquiring company to benefit from the established expertise and market position of the acquired entity. However, acquisitions often come with high upfront costs and significant integration challenges, such as cultural clashes and the need to align differing business practices.
In contrast, an in-house build strategy involves a company developing new capabilities or products internally rather than purchasing them. This method is also applicable to backward integration, as the company can start producing its own raw materials or components. For instance, a watch manufacturer might invest in developing its own facility to produce watch movements, ensuring that the designs and processes align perfectly with its brand’s requirements. The main benefits of building in-house include potentially lower long-term costs and the development of proprietary expertise and technologies. However, this strategy can be time-consuming and resource-intensive, requiring significant investment in research and development, as well as skilled personnel. There is also a higher risk of failure if the company lacks the necessary expertise or misjudges market demand.
Both acquisition and in-house build strategies are effective ways to achieve backward integration, each with its own set of benefits and challenges. An acquisition offers quick integration of capabilities at a higher initial cost and potential for complex assimilation, while an in-house build allows for customized development but demands considerable time and resources. The choice between the two depends on the company’s resources, time constraints, and long-term strategic goals.
Backward Integration vs Forward Integration
Backward integration and forward integration are two strategic approaches to gaining more control over the supply chain. Backward integration involves a company expanding its operations to produce its own raw materials or components, effectively taking over its suppliers. This can lead to cost savings, improved quality control, and a more reliable supply chain. For example, a watch manufacturer might acquire a company that makes watch movements to ensure a steady supply of these critical parts.
On the other hand, forward integration is when a company moves closer to the end customer by taking over distribution channels or retail outlets. This strategy allows the company to control the sales process, improve customer service, and potentially capture higher profit margins. For instance, a watch manufacturer might open its own branded retail stores or acquire an online platform to sell its products directly to consumers.
Both strategies aim to increase control and efficiency but focus on different parts of the supply chain. While backward integration secures inputs and production, forward integration enhances market presence and customer reach.
Backward Integration vs Vertical Integration
Backward integration is a specific type of vertical integration where a company expands its operations to produce its own raw materials or components, effectively taking control of its suppliers. This strategy aims to reduce costs, ensure a steady supply of inputs, and enhance quality control. For example, a watch manufacturer might acquire a company that produces watch movements to secure a reliable supply of these essential components.
Vertical integration, on the other hand, encompasses both backward and forward integration. It refers to a company’s efforts to control multiple stages of its production and distribution process, from raw materials to final product sales. This means that a company not only integrates backward by acquiring suppliers but also integrates forward by acquiring distributors or retailers. For instance, a vertically integrated watch manufacturer might own the companies that produce the watch components and also operate its own branded retail stores.
In essence, while backward integration focuses solely on securing the supply chain, vertical integration aims to streamline and control the entire production and distribution process, providing a comprehensive strategy for efficiency and market control.
FAQs of Backward Integration
1. How does backward integration affect cost efficiency?
It reduces costs by eliminating supplier markups and ensuring a steady, controlled supply of inputs.
2. Can backward integration improve product quality?
Yes, it allows for stringent quality control measures directly overseen by the company.
3. What financial risks are associated with backward integration?
The high initial investment and potential inefficiencies in managing an expanded supply chain pose financial risks.
4. How does backward integration impact supplier relationships?
It can strain existing supplier relationships and eliminate the benefits of supplier specialization and expertise.
5. Is backward integration suitable for all industries?
Not necessarily; its suitability depends on the industry, company size, and specific business goals.
6. How does backward integration foster innovation?
Companies can experiment with new processes and technologies more freely by having control over production.
7. What is the difference between backward integration and vertical integration?
Backward integration focuses on acquiring suppliers, while vertical integration includes both backward (suppliers) and forward (distributors/retailers) expansion.
8. Can backward integration lead to market expansion?
Indirectly, by improving efficiency, reducing costs, and potentially enhancing product offerings, it can support market expansion.
9. How does backward integration relate to competitive advantage?
It can provide a competitive edge through cost savings, improved quality, and control over critical production inputs.
Recommended Articles:
- Vertical Integration